- 1. EtherCAT Based Motion Control
-
Ezi-SERVOⅡ EtherCAT MINI is stepping motor control system using EtherCAT, high speed ethernet (100Mbps Full-Duplex) based fieldbus. Ezi-SERVOⅡ EtherCAT is EtherCAT slave module which support CAN application layer over EtherCAT (CoE). CiA 402 Drive Profile implemented. Supported modes are Profile Position Mode, Homing Mode, Cyclic Synchronous Position Mode.
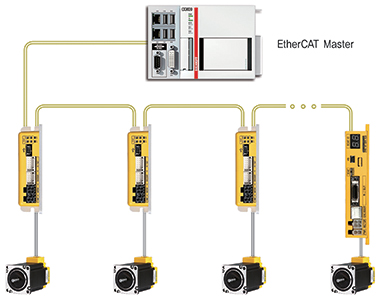
- 2. Closed Loop System
-
Ezi-SERVOⅡ is an innovative Closed Loop System that utilizes a high-resolution motor mounted encoder constantly to monitor the current position. The encoder feedback allows the Ezi-SERVOⅡ to update the current position every 50 micro seconds. It allows the Ezi-SERVOⅡ drive to compensate for the loss of position, ensuring accurate positioning. For example, due to a sudden load change, a conventional stepper motor and drive could lose a step but Ezi-SERVOⅡ automatically correct the position by encoder feedback.
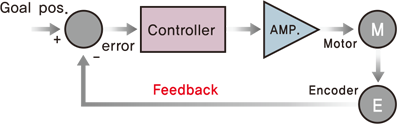
- 3. No Gain Tuning
-
To ensure machine performance, smoothness, positional error and low servo noise, conventional servo systems require the adjustment of its servo’s gains as an initial crucial step. Even systems that employ auto-tuning require manual tuning after the system is installed, especially if more that one axis are interdependent. Ezi-SERVOⅡ employs the best characteristics of stepper, closed loop motion controls and algorithms to eliminate the need of tedious gain tuning required for conventional closed loop servo systems. This means that Ezi-SERVOⅡ is optimized for the application and ready to work right out of the box. The Ezi-SERVOⅡ system employs the unique characteristics of the closed loop stepping motor control, eliminating these cumbersome steps and giving the engineer a high performance servo system without wasting setup time. Ezi-SERVOⅡ is especially well suited for low stiffness loads (for example, a belt and pulley system) that sometime require conventional servo systems to inertia match with the additimal expensive and bulky gearbox. Ezi-SERVOⅡ also performs exceptionally, even under heavy loads and high speeds.
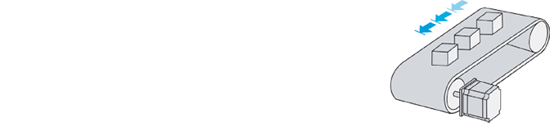
- 4. Heat Reduction / Energy Saving(Motor Current Control according to load)
-
Ezi-SERVOⅡ automatically controls motor current according to load. Ezi-SERVOⅡ reduces motor current when motor load is low and increases motor current when load is high. By optimizing the motor current, motor heat can be minimized and energy can be saved.
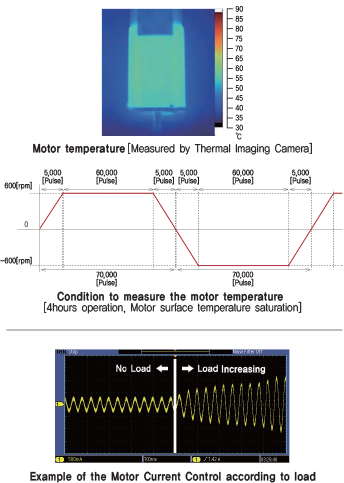
- 5. Torque Improvement(Motor Current Setting)
-
Ezi-SERVOⅡ can increase the motor current up to 150% by setting the Run Current by parameter. Therefore, acceleration and deceleration characteristics and torque characteristics at low speed can be increased.
Ezi-SERVOⅡ can improve the torque in the low speed range by about 30%.
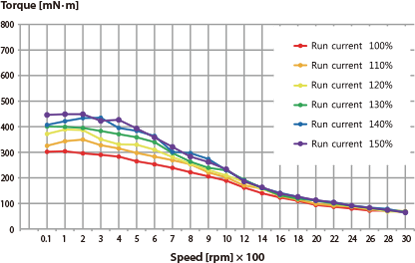
-
※ The torque at low speed is improved about 30%.
Measured Condition : Drive = Ezi-SERVOⅡ-EC-MI-42L
Motor Voltage = 24VDC
Input Voltage = 24VDC
- 6. No Hunting
-
Traditional servo motor drives overshoot their position and try to correct overshooting by moving the opposite direction, especially in high gain applications. This is called null hunt and is especially prevalent in systems that the break away or static friction is significantly higher than the running friction. The cure is lowering the gain, which affects accuracy or using Ezi-SERVOⅡ Motion Control System. Ezi-SERVOⅡ utilizes the unique characteristics of stepping motors and locks itself into the desired target position, eliminating Null Hunt. This feature is especially useful in applications such as nanotech manufacturing, semiconductor fabrication, vision systems and ink jet printing in which system oscillation and vibration could be a problem.
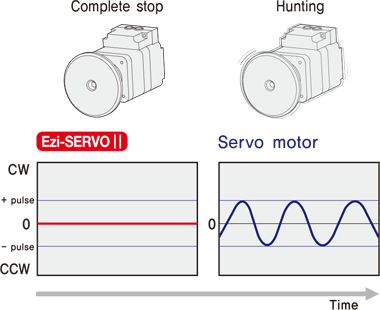
- 7. Smooth and Accurate
-
Ezi-SERVOⅡ is a high-precision servo drive, using a high-resolution encoder with 20,000 pulses/revolution. Unlike a conventional Microstep drive, the on-board high performance MCU (Micro Controller Unit) performs vector control and filtering, producing a smooth rotational control with minimum ripples.
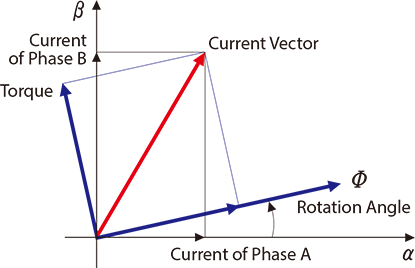
- 8. Fast Response
-
Similar to conventional stepping motors, Ezi-SERVOⅡ instantly synchronizes with command pulses providing fast positional response. Ezi-SERVOⅡ is the optimum choice when zero-speed stability and rapid motions within a short distance are required. Traditional servo motor systems have a natural delay called settling time between the command input signals and the resultant motion because of the constant monitoring of the current position.
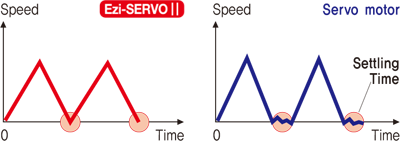
- 9. High Resolution
-
The unit of the position command can be divided precisely.
(Max. 20,000 pulses/revolution)
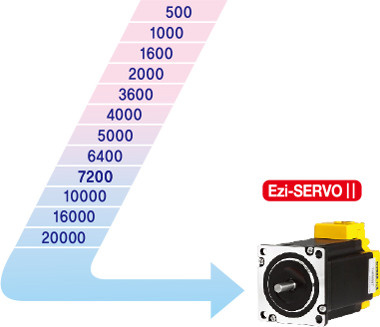
- 10. High Torque
-
Compared with common step motors and drives, Ezi-SERVOⅡ motion control systems can maintain a high torque state over relatively long period of time. This means that Ezi-SERVOⅡ continuously operates without loss of position under 100% of the load. Unlike conventional Microstep drives, Ezi-SERVO exploits continuous high torque operation during high speed motion due to its innovative optimum current phase control.
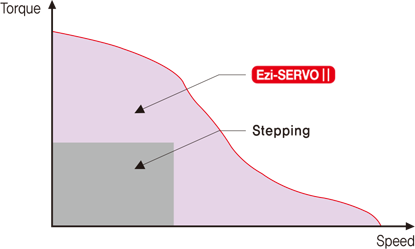
- 11. High Speed
-
The Ezi-SERVOⅡ operates well at high speed without the loss of synchronism or positioning error. Ezi-SERVO’s ability of continuous current position monitoring of enables the stepping motor to generate high torque, even under a 100% load condition.
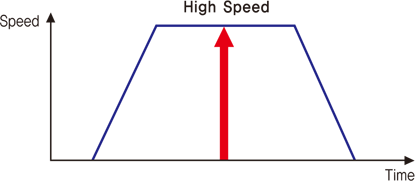
Advantages over Open-Loop Control Stepping Drive
1. Reliable positioning without loss of synchronism.
2. Holding stable position and automatically recovering to the original position even after experiencing positioning error due to external forces, such as mechanical vibration or vertical positional holding.
3. Ezi-SERVOⅡ utilizes 100% of the full range of rated motor torque, contrary to a conventional open-loop stepping driver that can use up to 50% of the rated motor torque due to the loss of synchronism.
4. Capability to operate at high speed due to load-dependant current control, open-loop stepping drivers use a constant current control at all speed ranges without considering load varitions.
Advantages over Servo Motor Controller
1. No gain tuning. (Automatic gain adjustment in response to a load change)
2. Maintains the stable holding position without oscillation after completion of positioning.
3. Fast positioning due to the independent control by on-board MCU.
4. Continuous operation during rapid short-stroke movement due to instantaneous positioning.